Tuotantoteknologia
Tiukka tuotantoprosessi ja korkean tarkkuuden tuotanto- ja testauslaitteet varmistavat tuotteiden korkean laadun.
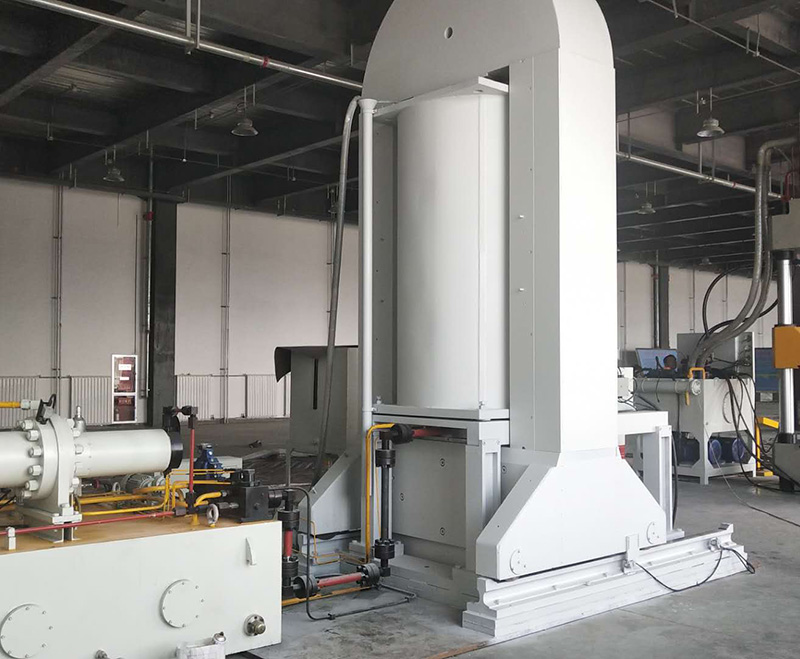
Kuivapuristusprosessi
Kuivapuristus on yksi laajimmin käytetyistä muovausprosesseista, tärkeimmät edut ovat korkea muovaustehokkuus, muotoiltujen tuotteiden pieni kokopoikkeama, joka sopii erityisen hyvin erilaisiin pieniin poikkileikkauspaksuuksiin keraamisiin tuotteisiin, kuten keraaminen venttiilin ydin, keraaminen levy, keraaminen rengas... jne.
Isostaattinen puristusprosessi ja ominaisuudet
Isostaattisella puristusmuovauksella on seuraavat edut teräspuristusmuovaukseen verrattuna:
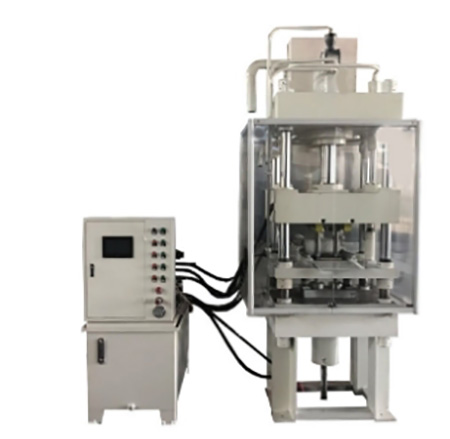
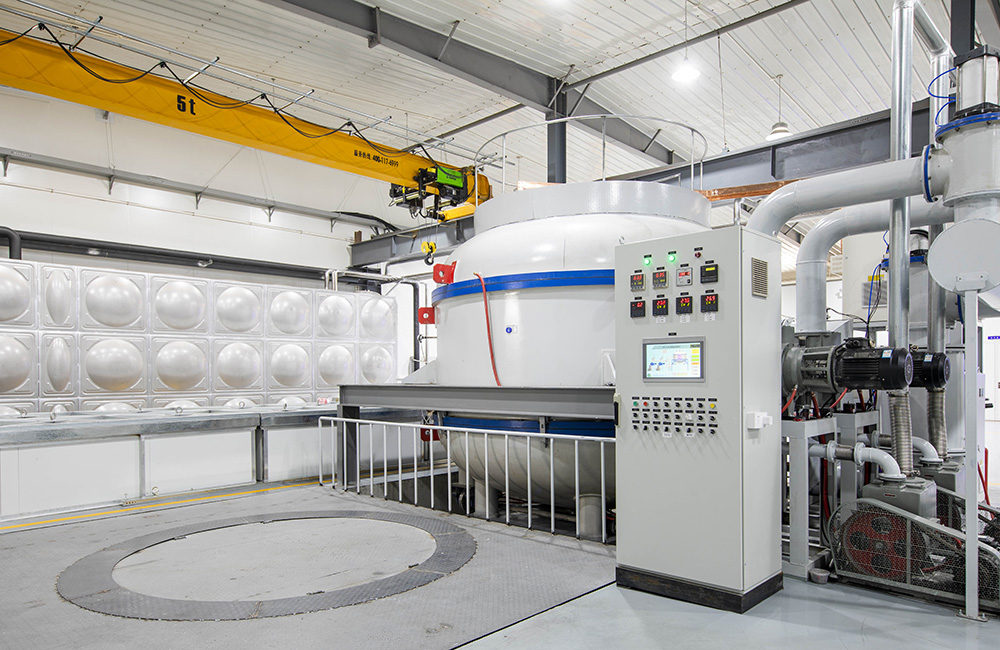
Keraaminen sintraus
Keraaminen aihio koostuu monista yksittäisistä kiinteistä hiukkasista ennen sintrausta, rungossa on suuri määrä huokosia, huokoisuus on yleensä 35 % ~ 60 % (eli aihion suhteellinen tiheys on 40 % ~ 65 %), spesifinen arvo riippuu itse jauheen ominaisuuksista ja käytetystä muovausmenetelmästä ja -tekniikasta. Kun kiinteää aihiota kuumennetaan korkeassa lämpötilassa, aihiossa olevat hiukkaset siirtyvät, tietyn lämpötilan saavuttamisen jälkeen aihio kutistuu, tapahtuu raekasvua, johon liittyy huokosten poistuminen, ja lopuksi aihiosta tulee tiheä monikiteinen keraaminen materiaali sulamispisteen alapuolella, tätä prosessia kutsutaan sintrautumiseksi.
Sisäinen ja ulkoinen pyöreä hionta
Sisä- ja ulompi pyöreä hionta (tunnetaan myös nimellä keskihionta) käytetään työkappaleen pyöreän ulkopinnan ja olakkeen hiomiseen. Työkappale on asennettu keskelle ja sitä pyöritetään keskiohjaimeksi kutsutulla laitteella. Hiomalaikkoja ja työkappaleita pyöritetään eri nopeuksilla erillisillä moottoreilla. Tuotteen kiinnitysasentoa voidaan säätää kulmaan suippenemisen aikaansaamiseksi. On olemassa viisi erilaista ulkohalkaisijan (OD) hiontaa, sisähalkaisijan (ID) hiontaa, rei'ityshiontaa, virumissyöttöhiontaa ja keskitöntä hiontaa.
Ulkohalkaisijan hionta
Ulkohalkaisijan hionta on hiontaa kohteen ulkopinnalla keskuksen ja keskustan välissä. Keskus on päätysolu, jossa on piste, joka sallii kohteen pyörimisen. Kun hiomalaikka koskettaa esinettä, myös hiomalaikka pyörii samaan suuntaan. Tämä tarkoittaa käytännössä sitä, että kun kaksi pintaa kosketetaan, ne liikkuvat vastakkaisiin suuntiin, mikä tekee toiminnasta vakaampaa ja vähemmän tukkeutumista.
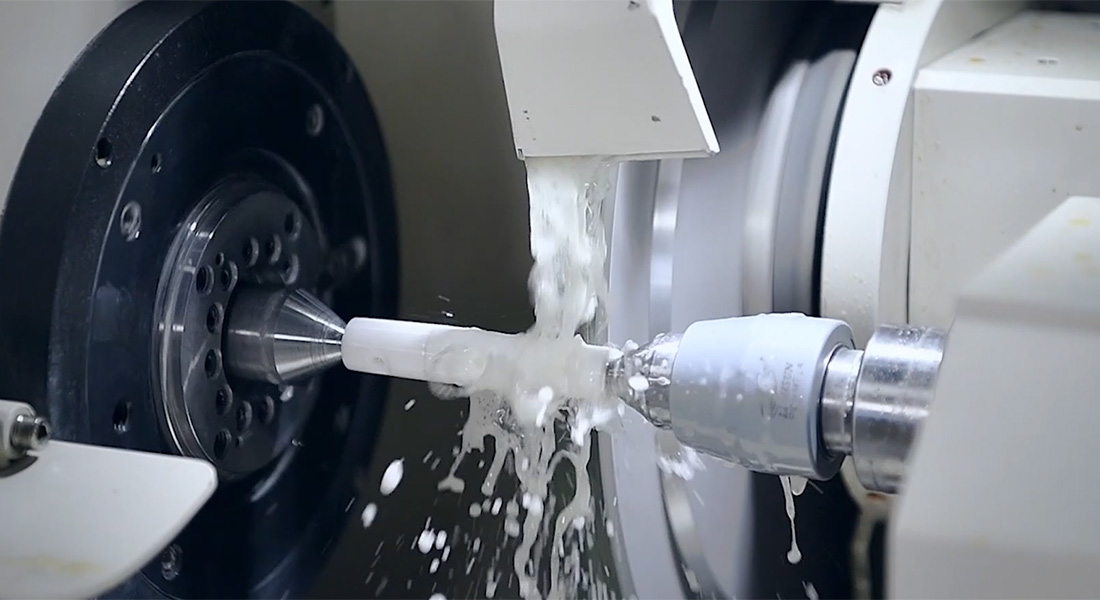
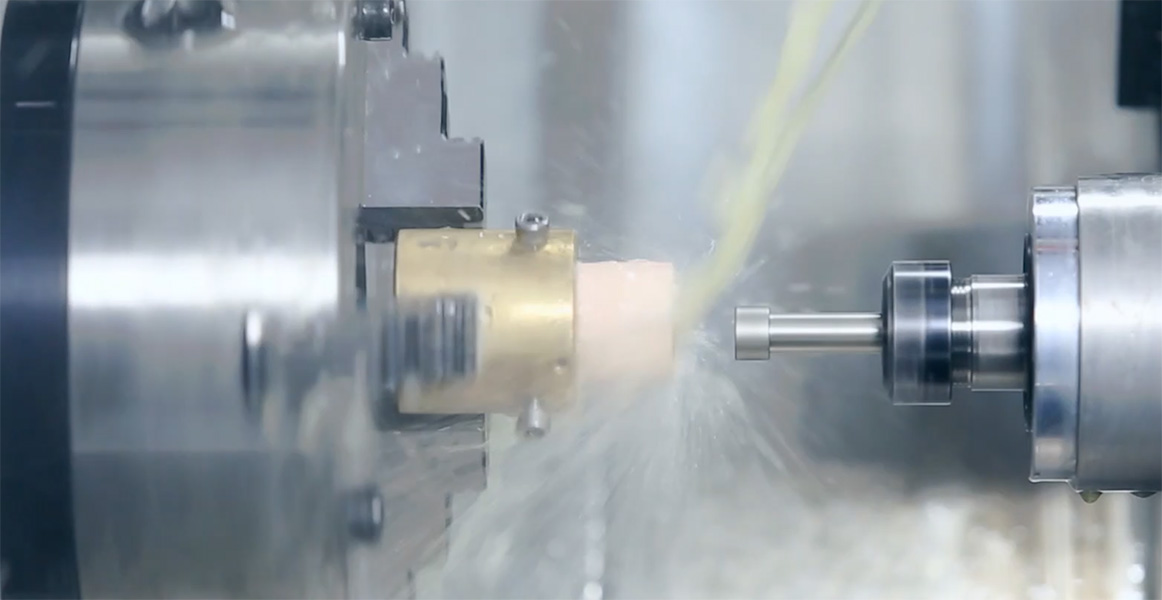
Sisähalkaisijan hionta
Sisähalkaisijahionta on hiontaa esineen sisällä. Hiomalaikan leveys on aina pienempi kuin esineen leveys. Valaisin pitää esineen paikallaan, joka myös kääntää kohteen paikalleen. Aivan kuten ulkohalkaisijahionnassa, pyörä ja esine pyörivät vastakkaisiin suuntiin siten, että hiontapinnan kosketussuunta on vastakkainen.
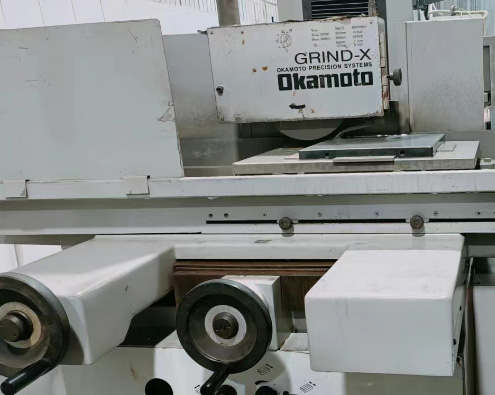
Tasainen hionta
Tasohionta on yleisin hiontatoiminto. Se on prosessointitekniikka, joka käyttää pyörivää hiomalaikkaa metallien tai ei-metallisten materiaalien pinnan hiomiseen oksidikerroksen ja epäpuhtauksien poistamiseksi työkappaleen pinnalta, jotta sen pinta olisi hienostuneempi. Tasohiomakone on työstökone, joka on suunniteltu tuottamaan tarkat hiomapinnat, olipa kyseessä kriittinen koko tai pinnan viimeistely. Litteän hiomakoneen tarkkuus riippuu sen tyypistä ja käytöstä, levyn halkaisija on 300 mm, planimetrinen tarkkuus voi olla 0,003 mm. Tasohiontaan suurin käsittelykoko: pituus 1600* leveys 800mm.
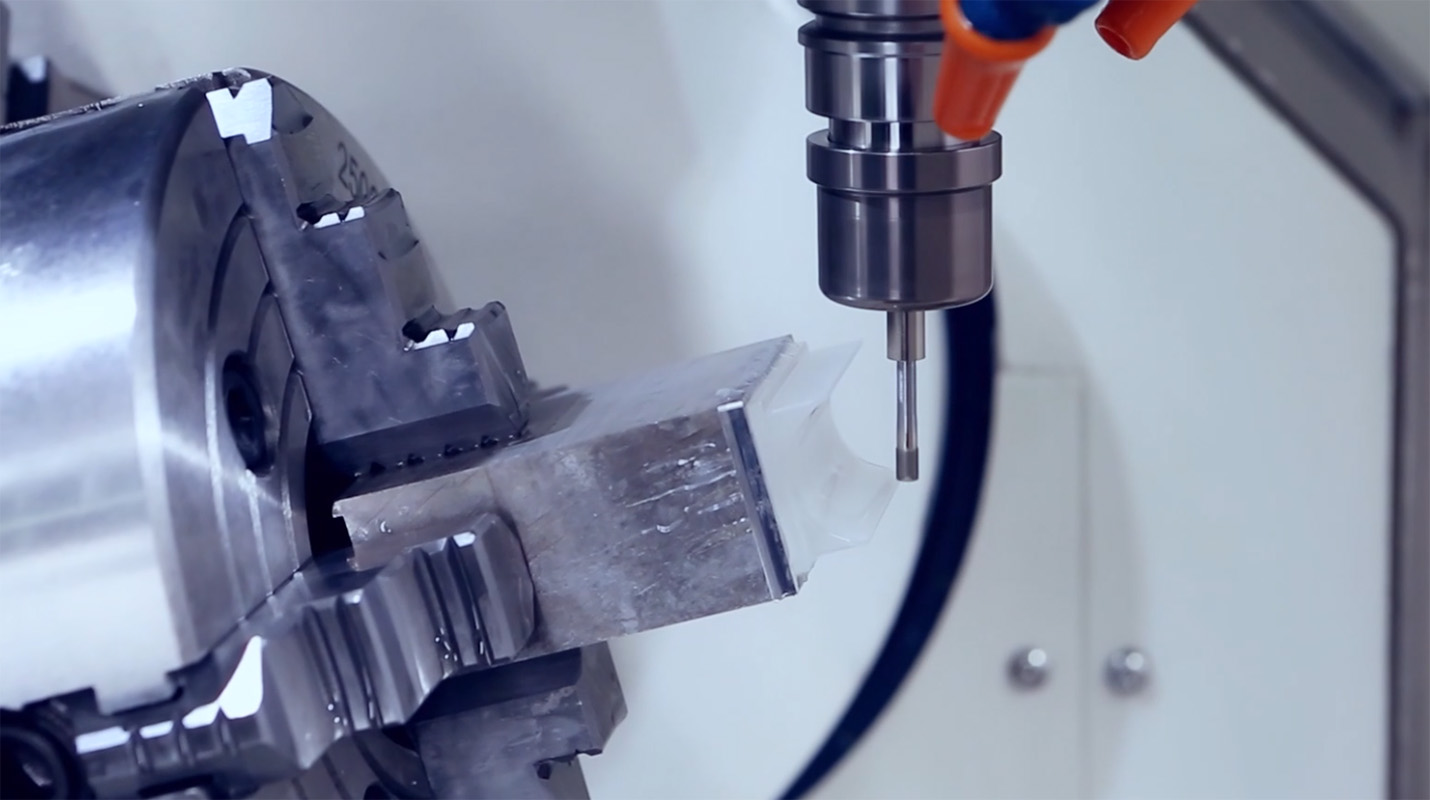
CNC
CNC-jyrsintää pidetään yhtenä koneistuksen yleisimmin käytetyistä operaatioista. CNC-jyrsintä on eräänlainen CNC-työstökone, jolla on vahva työstötoiminto, nopeasti kehittynyt koneistuskeskus, joustava työstöyksikkö jne. valmistetaan CNC-jyrsinkoneen ja CNC-porauskoneen pohjalta, molemmat ovat erottamattomia jyrsintämenetelmästä, useimmat teolliset jyrsintätyöt voidaan suorittaa 3-akselisilla, 5-akselisilla CNC-työstökoneilla. Vahvan mukautumiskyvyn, korkean käsittelytarkkuuden, vakaan prosessoinnin laadun ja korkean tuotantotehokkuuden etujen ansiosta tämäntyyppinen polkuohjaus voi käsitellä jopa 80 % mekaanisista osista. CNC:llä on suurin koneistuskoko: pituus 1300* leveys 800 mm.
Puolijohdekomponenttien puhdistusprosessi
Märkäpuhdistus
Märkäpuhdistus tarkoittaa kemiallisten liuottimien tai deionisoidun veden käyttöä kiekon puhdistamiseen. Märkäpuhdistus voidaan jakaa liotusmenetelmään ja ruiskutusmenetelmään prosessimenetelmän mukaan, liotusmenetelmä on upottaa kiekko säiliöön, joka sisältää kemiallista liuotinta tai deionisoitua vettä. Liotusmenetelmä on laajalti käytetty menetelmä, erityisesti joissakin kypsissä solmuissa. Toisaalta ruiskutukseen kuuluu kemiallisen liuottimen tai deionisoidun veden suihkuttaminen pyörivälle kiekolle epäpuhtauksien poistamiseksi. Liotusmenetelmällä voidaan käsitellä useita kiekkoja samanaikaisesti, ja ruiskutusmenetelmällä voidaan käsitellä vain yhtä kiekkoa yhdessä työkammiossa samanaikaisesti. Prosessin kehittymisen myötä puhdistusprosessin vaatimukset ovat yhä korkeammat ja ruiskutusmenetelmän käyttö laajenee.
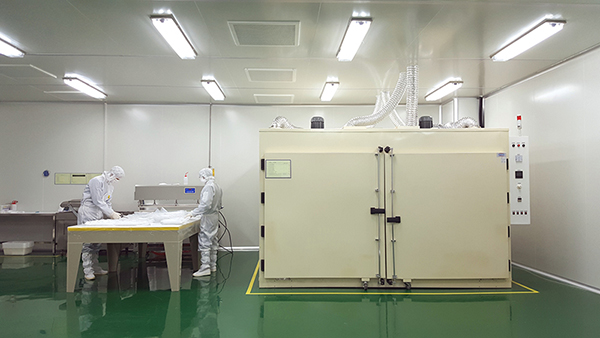
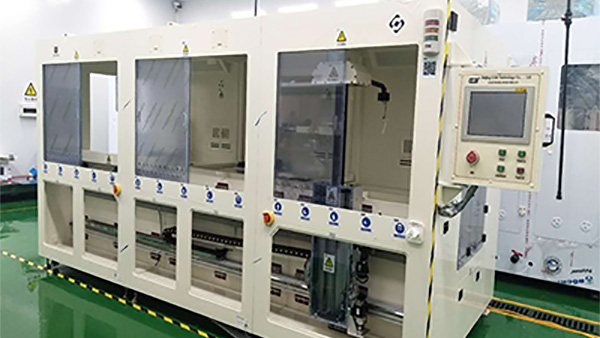
Kuivapesu
Kuten nimestä voi päätellä, kuivapesu ei ole kemiallisten liuottimien tai deionisoidun veden käyttöä, vaan kaasun tai plasman käyttöä puhdistukseen. Teknisten solmujen jatkuvan kehittymisen myötä puhdistusprosessin vaatimukset kohoavat jatkuvasti, myös käytön osuus kasvaa, ja myös märkäpuhdistuksesta syntyvä jäteneste kasvaa voimakkaasti. Märkäpuhdistukseen verrattuna kuivapesulla on korkeat investointikustannukset, monimutkainen laitteiden käyttö ja ankarammat puhdistusolosuhteet. Kuitenkin joidenkin orgaanisten yhdisteiden ja nitridien, oksidien poistamiseksi kuivapesun tarkkuus on korkeampi, vaikutus on erinomainen.
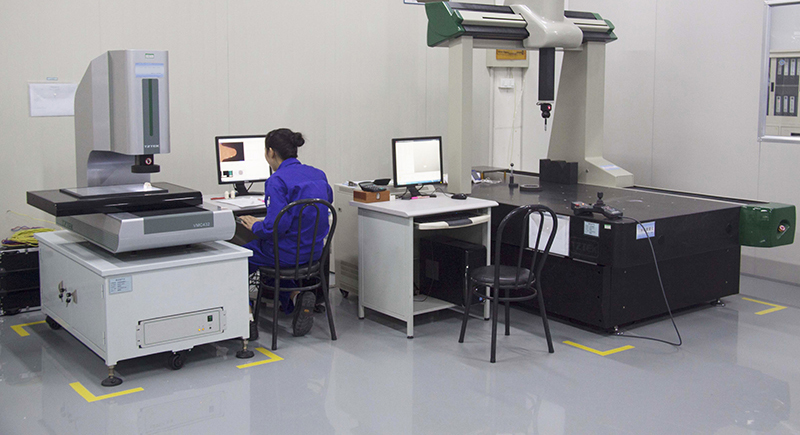
Tarkkuusmittaus
Meillä on kykyjä materiaalitutkimuksessa, tuotekehityksessä, suunnittelussa, valmistuksessa ja laadunhallinnassa, ja meillä on täydellinen valikoima tarkkuustyöstö- ja testauslaitteita: kolme koordinaattia, karheusmittari, samankeskisyysmittari, ulkohalkaisijan mittauslaite, tarkkuustestauslaitteiden sylinterimäisyysmittari. Tiukka tuotantoprosessi ja korkean tarkkuuden tuotanto- ja testauslaitteet varmistavat tuotteiden korkean laadun.
DLC-pinnoite
Kiekkokannatin/tarttujapöytiä käytetään sisältämään Si-, SiC-, GaAs-, Gan- ja muita puolijohdekiekkoja erilaisissa puolijohdeprosesseissa detektiosta litografiaan ja muissa erittäin tarkasti vaativissa sovelluksissa, mukaan lukien suurten, ohuiden joustavien litteiden näyttöjen kotelo. , MEMS ja biologiset solut. DLC-pinnoitteilla on monia toivottavia ominaisuuksia, kuten kestävä kestävyys ja korkea lämmönjohtavuus, jotka maksimoivat tuotteen käyttöiän, säilyttävät tarkkuuden ja vähentävät kitkaa ja kontaminaatiota. Tyhjiötarttuja koostuu jäykästä rungosta, jossa on useita tarttuja kiekon tai paneelin pinnalla, ja kokonais- ja paikallistasoisuuden poikkeama mitataan nanometreinä, tässä tapauksessa ongelmana on DLC-pinnoitteen levittäminen koko pinnan pinnalle. tarttuja on se, että lämpölaajenemisen epäsovitus voi johtaa tasaisuuden menettämiseen.
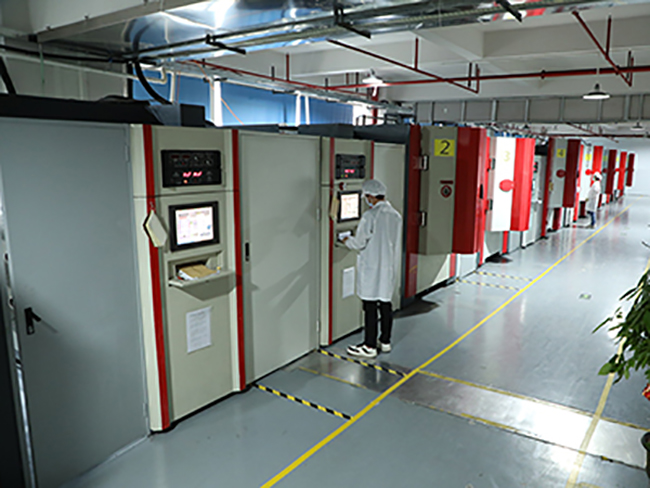
Teflon™ fluoripolymeeri puolijohteiden valmistukseen
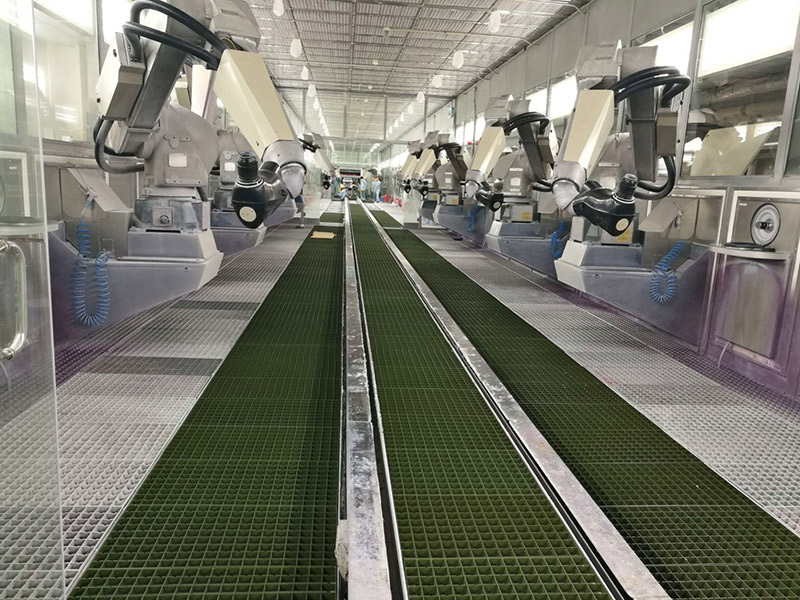