Gyártástechnológia
Szigorú gyártási folyamat és nagy pontosságú gyártási és tesztelő berendezések a termékek magas minőségének biztosítása érdekében.
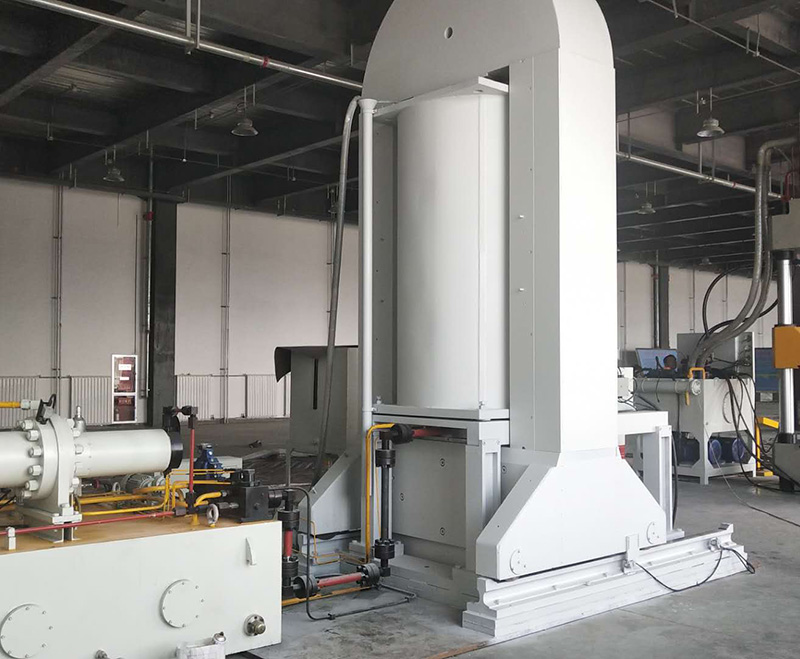
Száraz préselési eljárás
A száraz sajtolás az egyik legszélesebb körben használt fröccsöntési eljárás, a fő előnyök a nagy öntési hatékonyság, a fröccsöntött termékek kis méretbeli eltérése, különösen alkalmas kerámiatermékek különféle kis keresztmetszetvastagságára, mint például kerámia szelepmag, kerámia lemez, kerámia. gyűrű...stb.
Izosztatikus préselési folyamat és jellemzők
Az izosztatikus présléc a következő előnyökkel rendelkezik az acél préseléssel szemben:
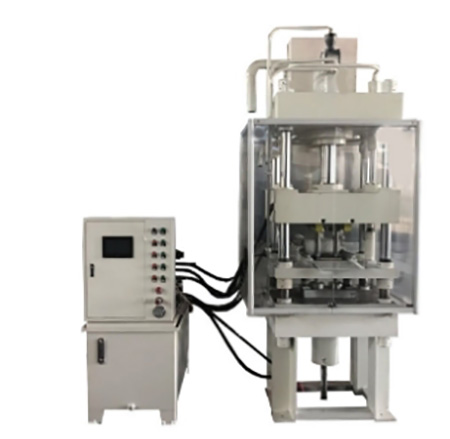
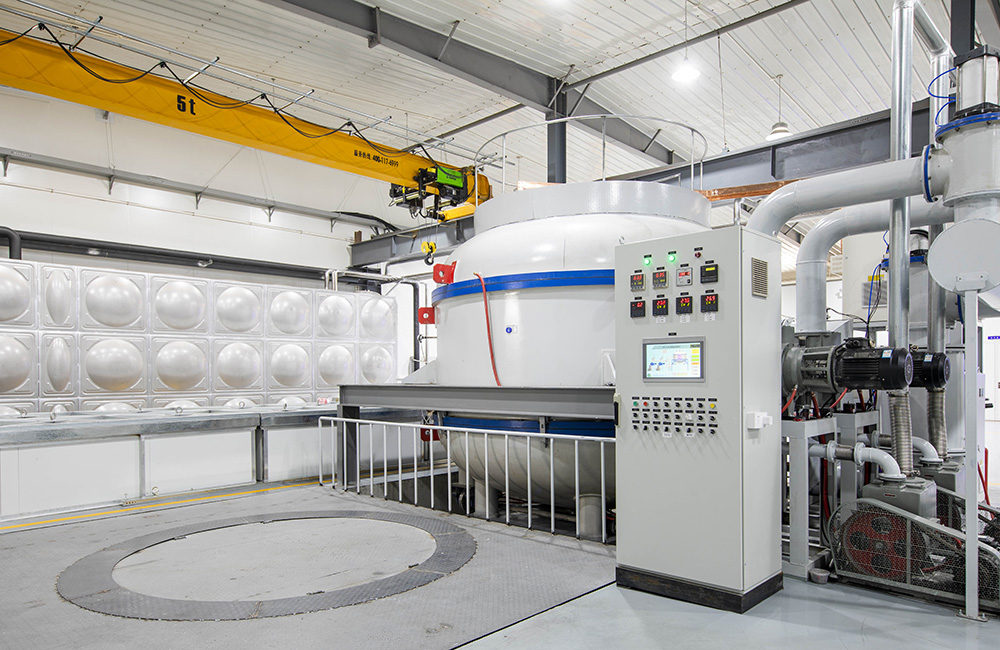
Kerámia szinterezés
A kerámia nyersdarab sok egyedi szilárd részecskéből áll a szinterezés előtt, nagyszámú pórus van a testben, a porozitás általában 35% ~ 60% (azaz a nyersdarab relatív sűrűsége 40% ~ 65%), a fajlagos érték magának a pornak a jellemzőitől, valamint az alkalmazott formázási módszertől és technológiától függ. Ha a szilárd nyersdarabot magas hőmérsékleten hevítjük, a nyersdarabban lévő részecskék átkerülnek, egy bizonyos hőmérséklet elérése után a nyersdarab összezsugorodik, szemcsenövekedés következik be, amit a pórusok eltűnése kísér, és végül a nyersdarab sűrű polikristály kerámia anyaggá válik az olvadáspont alatti hőmérsékletet, ezt a folyamatot szinterezésnek nevezik.
Belső és külső körkörös köszörülés
A belső és külső körkörös köszörülés (más néven középső köszörülés) a munkadarab külső körfelületének és vállának köszörülésére szolgál. A munkadarab a közepére van felszerelve, és egy központi meghajtónak nevezett eszköz forgatja. A csiszolókorongokat és a munkadarabokat különálló motorok különböző sebességgel forgatják. A termék rögzítési helyzete szögben állítható, hogy kúpos legyen. Ötféle külső átmérőjű (OD), belső átmérőjű (ID) köszörülés, lyukasztó köszörülés, kúszótakarmány köszörülés és középpont nélküli köszörülés létezik.
Külső átmérőjű csiszolás
A külső átmérőjű köszörülés egy tárgy külső felületének köszörülése a közepe és a közepe között. A középpont egy végcella egy ponttal, amely lehetővé teszi az objektum elforgatását. Amikor a köszörűkorong érintkezik a tárggyal, a csiszolókorong is ugyanabba az irányba forog. Ez gyakorlatilag azt jelenti, hogy érintkezéskor a két felület ellentétes irányba mozog, ami stabilabbá teszi a működést és kevésbé blokkolja.
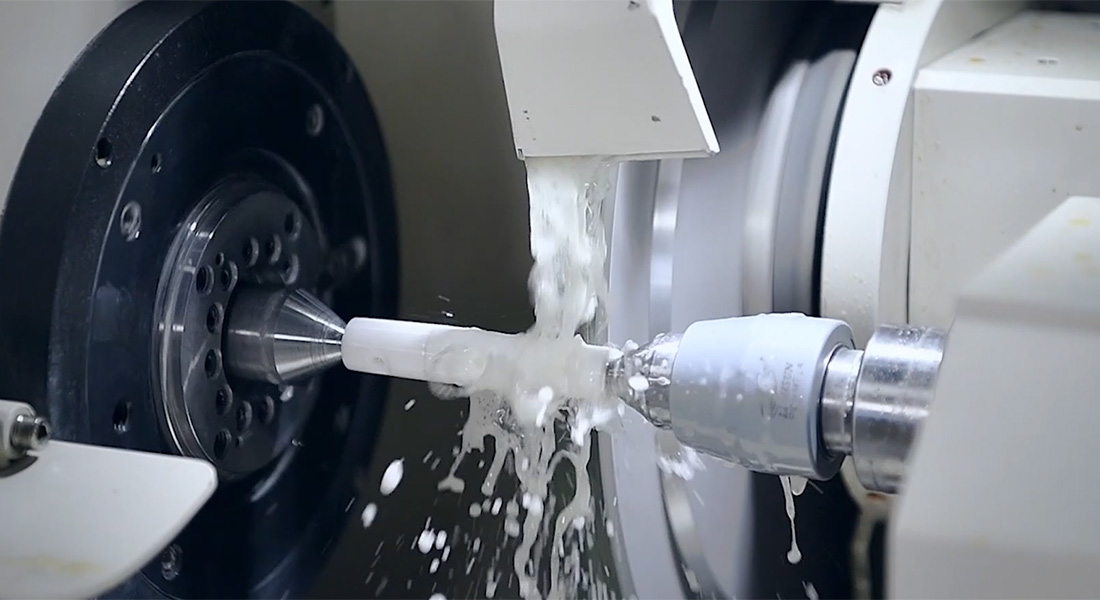
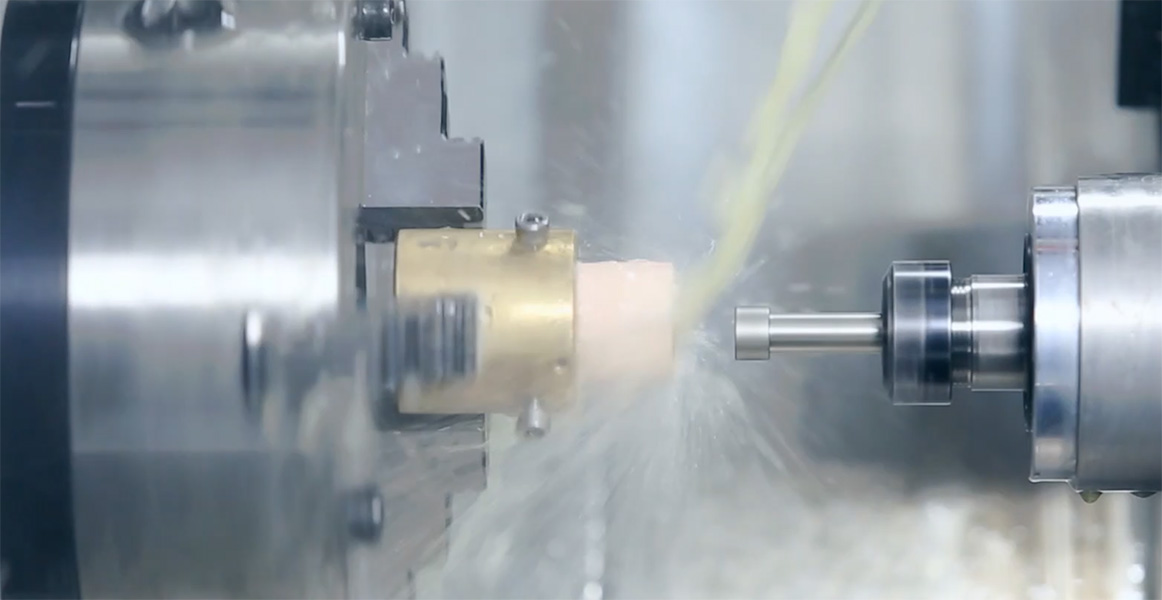
Belső átmérőjű csiszolás
A belső átmérőjű köszörülés egy tárgy belsejében történő köszörülés. A csiszolókorong szélessége mindig kisebb, mint a tárgy szélessége. A tárgyat a fixture tartja a helyén, amely a tárgyat a helyén is elforgatja. A külső átmérőjű köszörüléshez hasonlóan a tárcsa és a tárgy ellentétes irányba forog, így a két felület érintkezési iránya, ahol a köszörülés történik, ellentétes.
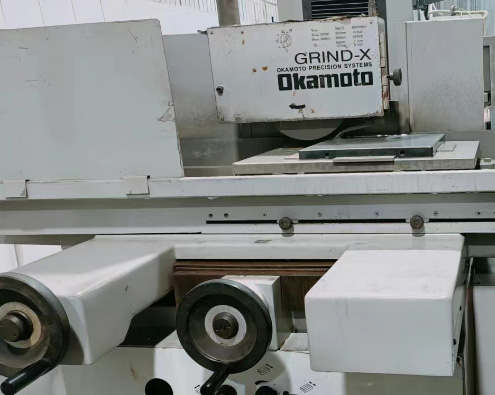
Lapos köszörülés
A lapos köszörülés a leggyakoribb köszörülési művelet. Ez egy olyan feldolgozási technológia, amely forgó csiszolókorongot használ a fém vagy nem fémes anyagok felületének csiszolására, hogy eltávolítsa az oxidréteget és a szennyeződéseket a munkadarab felületéről, így a felület finomabbá válik. A lapos csiszoló egy olyan szerszámgép, amelyet arra terveztek, hogy pontos csiszolási felületet biztosítson, legyen szó kritikus méretről vagy felületkikészítésről. A lapos csiszoló fajlagos pontossága típusától és felhasználásától függ, átmérője 300 mm-es tárcsa, a planimetrikus pontosság elérheti a 0,003 mm-t. A lapos csiszolás maximális megmunkálási mérete: hossz 1600* szélesség 800 mm.
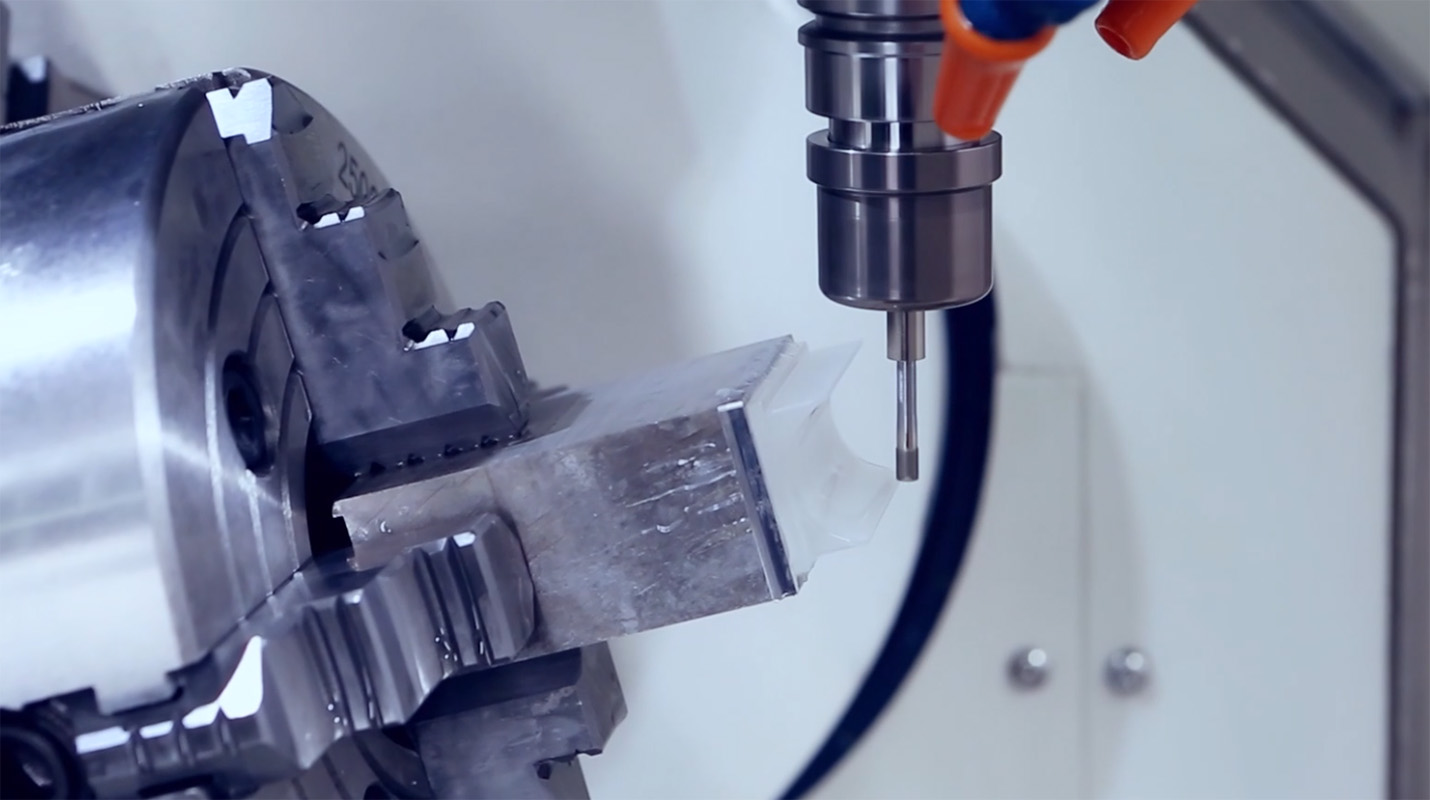
CNC
A CNC marás a megmunkálás egyik legszélesebb körben alkalmazott művelete. A CNC marás egyfajta CNC szerszámgép erős megmunkáló funkcióval, a gyorsan fejlődő megmunkáló központ, rugalmas megmunkáló egység stb. CNC marógép és CNC fúrógép alapján készül, mindkettő elválaszthatatlan a marási módszertől, a legtöbb ipari a marási műveletek 3 tengelyes, 5 tengelyes CNC szerszámgépekkel végezhetők el. Az erős alkalmazkodóképesség, a nagy feldolgozási pontosság, a stabil feldolgozási minőség és a magas gyártási hatékonyság előnyei révén ez a fajta útvezérlés a mechanikai alkatrészek akár 80%-át is képes feldolgozni. A CNC maximális megmunkálási mérete: hossz 1300* szélesség 800 mm.
Félvezető alkatrészek tisztítási folyamata
Nedves tisztítás
A nedves tisztítás kémiai oldószerek vagy ioncserélt víz használata az ostya tisztítására. A nedves tisztítás az eljárási módszer szerint áztatási módszerre és permetezési módszerre osztható, az áztatási módszer az, hogy az ostyát vegyi oldószert vagy ionmentesített vizet tartalmazó tartályba merítsük. Az áztatási módszer széles körben alkalmazott módszer, különösen néhány érett csomópont esetében. A permetezés ezzel szemben kémiai oldószert vagy ionmentesített vizet permetez egy forgó ostyára a szennyeződések eltávolítása érdekében. Az áztatási módszerrel egyszerre több ostya, a permetezéssel pedig egy munkakamrában egyszerre csak egy ostyát lehet feldolgozni. Az eljárás fejlődésével a tisztítási eljárással szemben támasztott követelmények egyre magasabbak, a permetezési mód alkalmazása pedig egyre kiterjedtebbé válik.
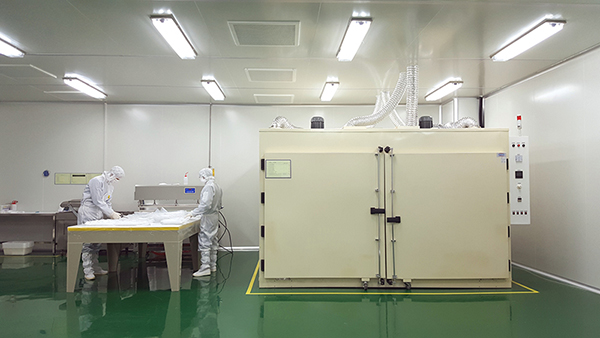
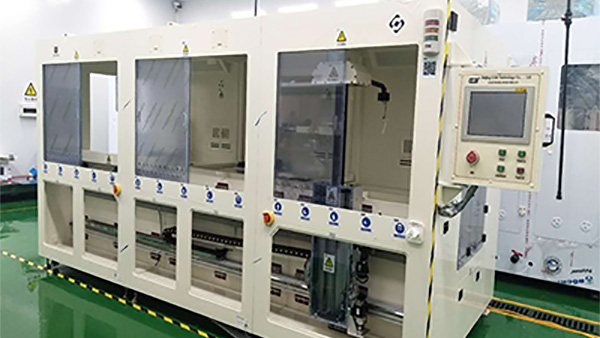
Száraz tisztítás
Ahogy a neve is sugallja, a vegytisztítás nem kémiai oldószerek vagy ioncserélt víz, hanem gáz vagy plazma használata a tisztításhoz. A műszaki csomópontok folyamatos fejlődésével a tisztítási folyamat követelményei egyre magasabbak, a felhasználás aránya is növekszik, és nagymértékben nő a nedves tisztítás során keletkező hulladékfolyadék is. A nedves tisztításhoz képest a vegytisztításnak magas a beruházási költsége, bonyolultabb a berendezés működése és keményebb tisztítási körülményei vannak. Egyes szerves vegyületek és nitridek, oxidok eltávolítására azonban nagyobb a vegytisztítási pontosság, a hatás kiváló.
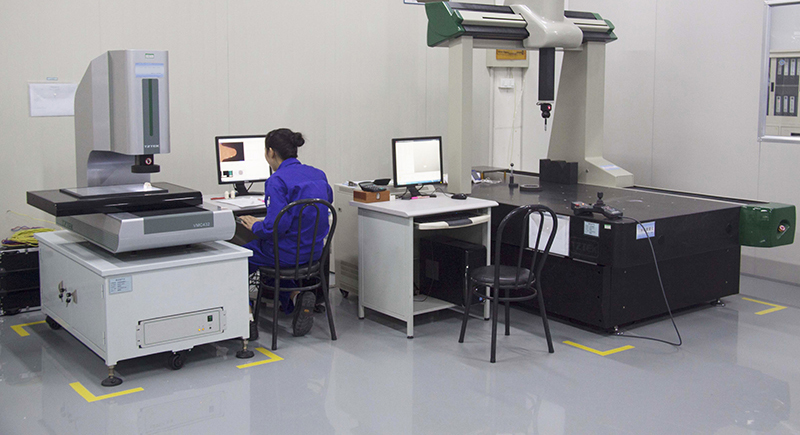
Precíziós mérés
Tehetségeink vannak az anyagkutatásban, a termékfejlesztésben, a tervezésben, a gyártásban és a minőségirányításban, valamint teljes precíziós megmunkáló és vizsgáló berendezéssel rendelkezünk: három koordináta, érdességmérő, koncentrikusságmérő, külső átmérőmérő műszer, hengerességmérő precíziós vizsgáló műszerek. Szigorú gyártási folyamat és nagy pontosságú gyártási és tesztelő berendezések a termékek magas minőségének biztosítása érdekében.
DLC bevonat
Az ostyahordozó/fogóasztalok Si, SiC, GaAs, Gan és más félvezető lapkák tárolására szolgálnak különféle félvezető eljárásokban, a detektálástól a litográfiáig, és más, nagy pontosságot igénylő alkalmazásokhoz, beleértve a nagy, vékony, rugalmas lapos kijelzők házát. , MEMS és biológiai sejtek. A DLC bevonatok számos kívánatos tulajdonsággal rendelkeznek, például tartós ellenállással és magas hővezető képességgel, hogy maximalizálják a termék élettartamát, megőrizzék a pontosságot, valamint csökkentsék a súrlódást és a szennyeződést. A vákuumfogó egy merev testből áll, több megfogóval az ostya vagy panel felületén, és a teljes és helyi síkság eltérését nanométerben mérik, ebben az esetben a probléma a DLC bevonat felvitele a teljes felületen. a megfogó az, hogy a hőtágulási eltérés a síkság elvesztéséhez vezethet.
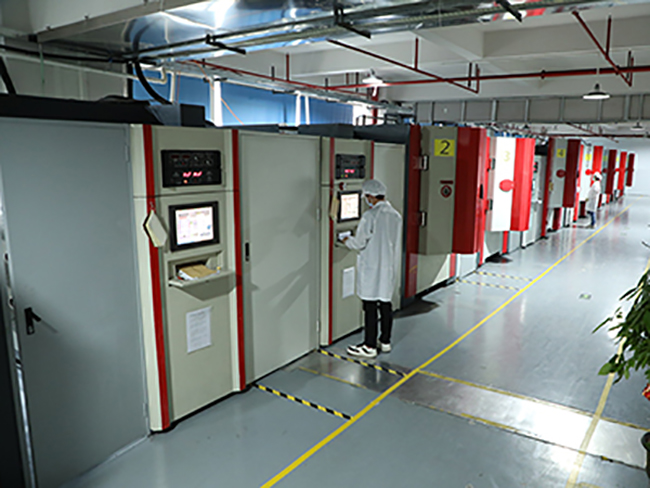
Teflon™ fluorpolimer félvezetőgyártáshoz
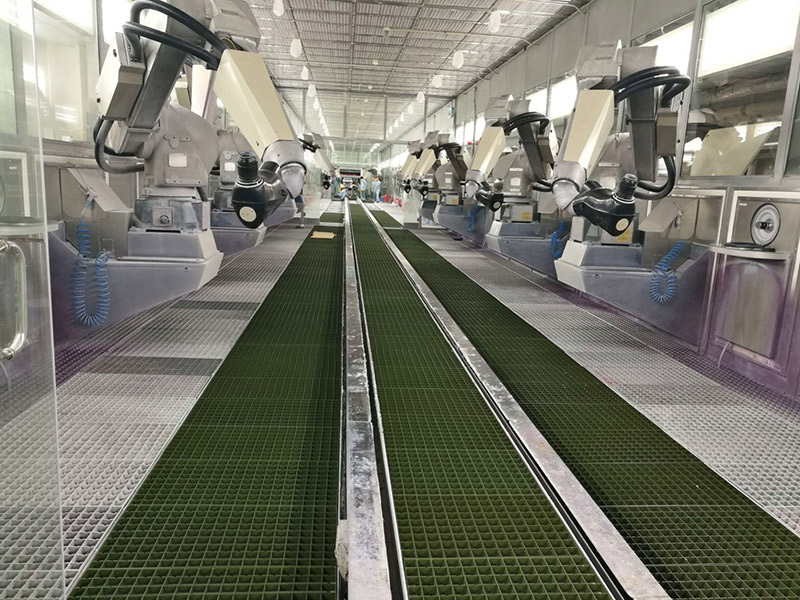