Tecnologia di produzione
Processo di produzione rigoroso e apparecchiature di produzione e collaudo ad alta precisione per garantire l'alta qualità dei prodotti.
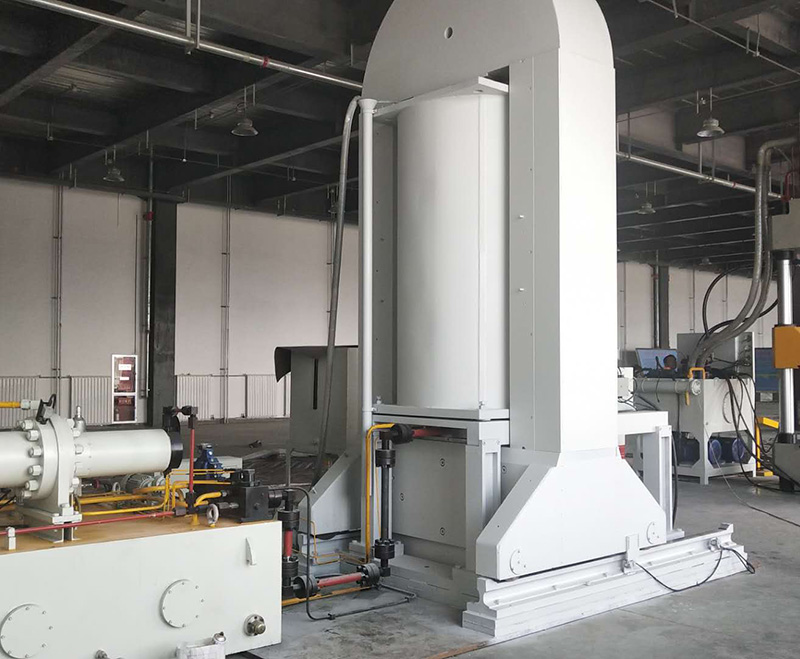
Processo di pressatura a secco
La pressatura a secco è uno dei processi di stampaggio più utilizzati, i principali vantaggi sono l'elevata efficienza di stampaggio, la deviazione di piccole dimensioni dei prodotti stampati, particolarmente adatta per una varietà di prodotti ceramici di piccolo spessore di sezione, come il nucleo della valvola in ceramica, la piastra in ceramica, la ceramica anello... ecc.
Processo e caratteristiche della pressatura isostatica
Lo stampaggio per pressatura isostatica presenta i seguenti vantaggi rispetto allo stampaggio per pressatura dell'acciaio:
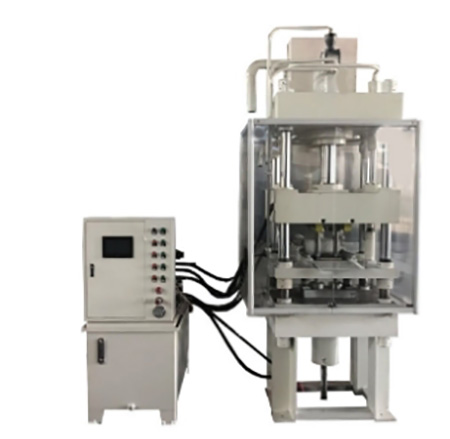
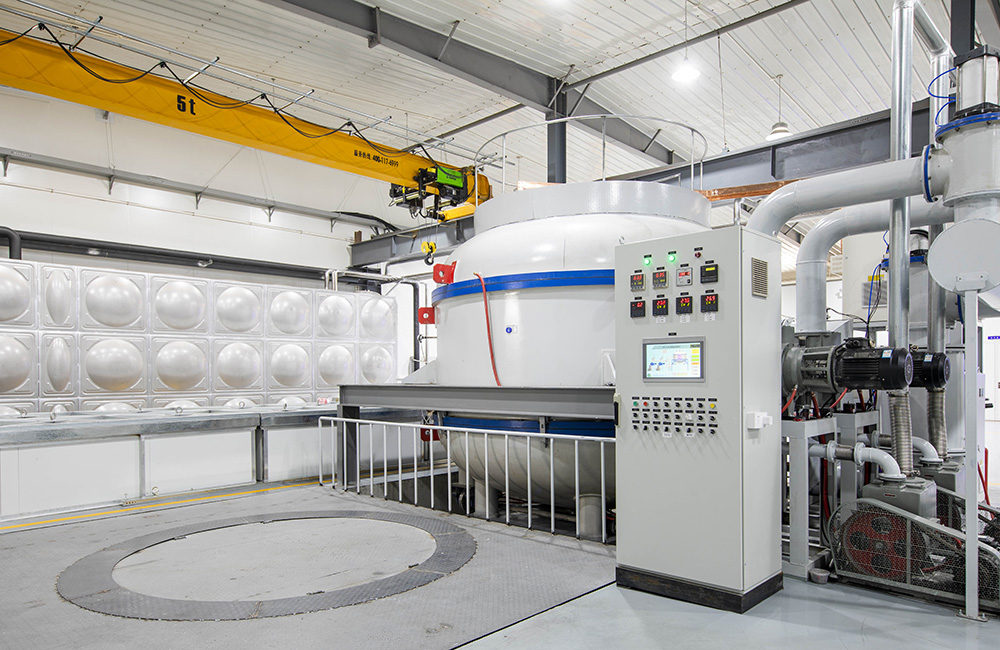
Sinterizzazione della ceramica
Il pezzo grezzo in ceramica è composto da molte singole particelle solide prima della sinterizzazione, nel corpo è presente un gran numero di pori, la porosità è generalmente del 35% ~ 60% (ovvero, la densità relativa del pezzo grezzo è del 40% ~ 65%), il valore specifico dipende dalle caratteristiche della polvere stessa e dal metodo e dalla tecnologia di stampaggio utilizzata. Quando il pezzo grezzo solido viene riscaldato ad alta temperatura, le particelle nel pezzo grezzo si trasferiscono, dopo aver raggiunto una certa temperatura, il pezzo grezzo si restringe, avviene la crescita dei grani, accompagnata dall'eliminazione dei pori, e infine il pezzo grezzo diventa un materiale ceramico policristallino denso a una temperatura inferiore al punto di fusione, questo processo è chiamato sinterizzazione.
Rettifica circolare interna ed esterna
La rettifica circolare interna ed esterna (nota anche come rettifica centrale) viene utilizzata per rettificare la superficie circolare esterna e la spalla del pezzo. Il pezzo è montato al centro e viene ruotato da un dispositivo chiamato driver centrale. Le mole e i pezzi vengono ruotati a velocità diverse da motori separati. La posizione di bloccaggio del prodotto può essere regolata ad angolo per produrre conicità. Esistono cinque tipi di rettifica del diametro esterno (OD), rettifica del diametro interno (ID), rettifica del punzone, rettifica con avanzamento lento e rettifica senza centri.
Rettifica diametri esterni
La rettifica del diametro esterno è la rettifica sulla superficie esterna di un oggetto tra il centro e il centro. Il centro è una cella terminale con un punto che consente all'oggetto di ruotare. Quando la mola è a contatto con l'oggetto, anche la mola ruota nella stessa direzione. Ciò significa effettivamente che quando vengono a contatto, le due superfici si muovono in direzioni opposte, il che rende l'operazione più stabile e meno bloccante.
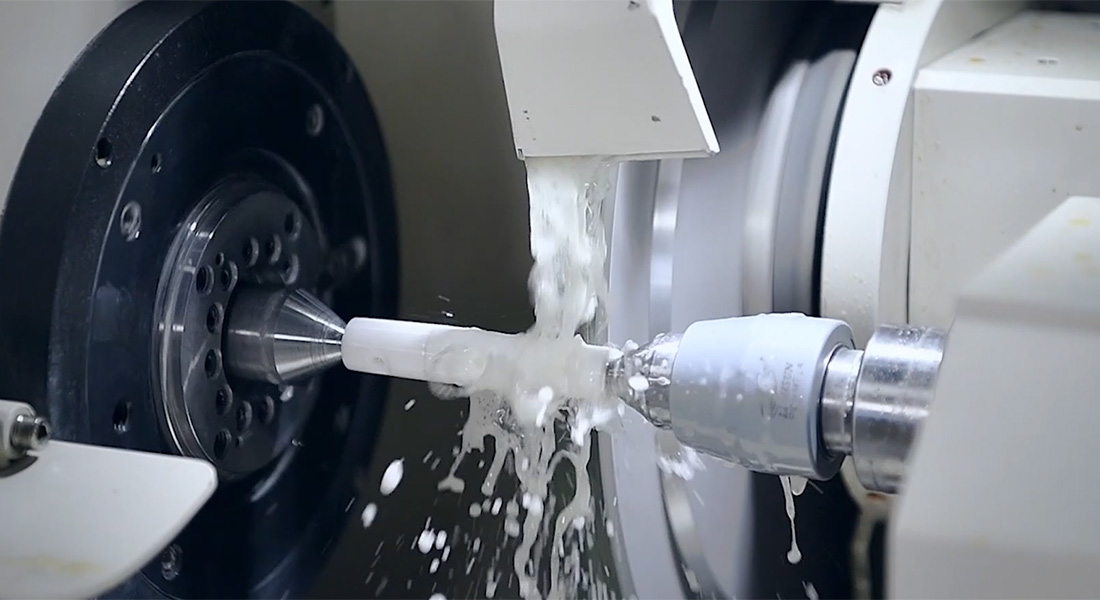
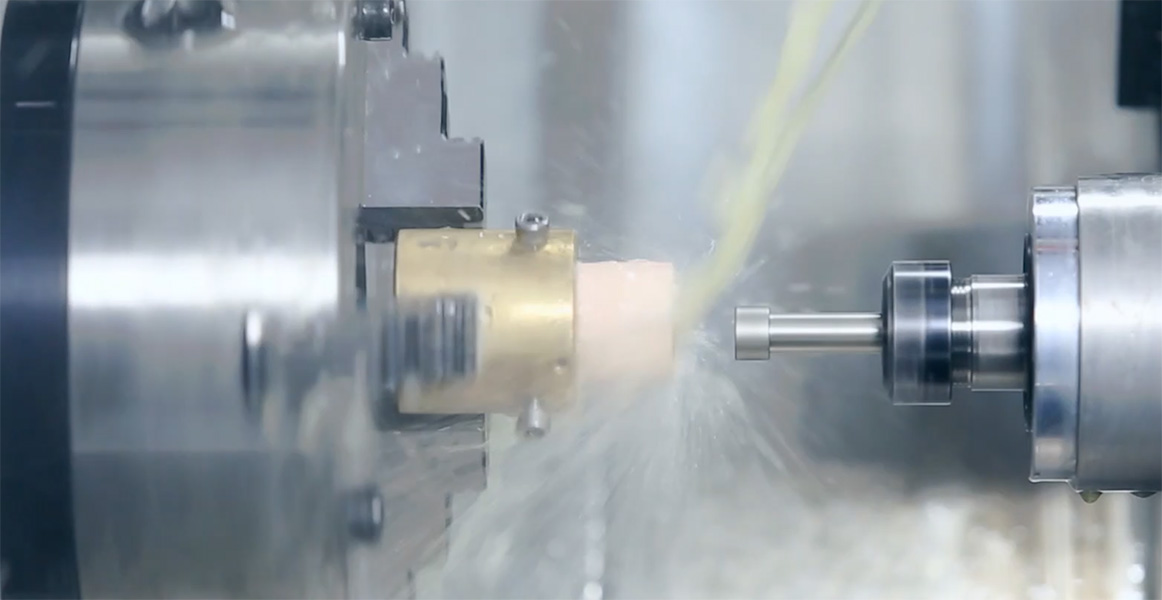
Rettifica del diametro interno
La rettifica del diametro interno è la rettifica all'interno di un oggetto. La larghezza della mola è sempre inferiore alla larghezza dell'oggetto. L'oggetto è tenuto in posizione dal dispositivo, che ruota anche l'oggetto in posizione. Esattamente come nella rettifica del diametro esterno, la mola e l'oggetto ruotano in direzioni opposte per cui il senso di contatto delle due superfici su cui avviene la rettifica è opposto.
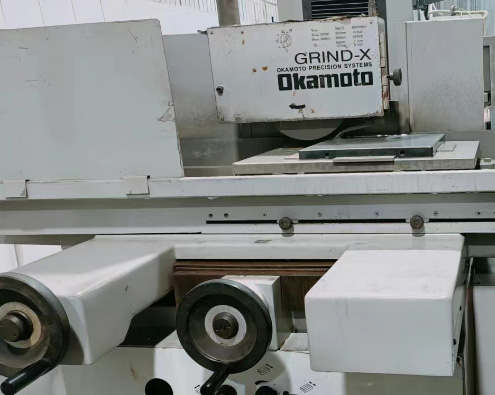
Rettifica piana
La rettifica in piano è l'operazione di rettifica più comune. È una tecnologia di lavorazione che utilizza una mola rotante per levigare la superficie di materiali metallici o non metallici per rimuovere lo strato di ossido e le impurità sulla superficie del pezzo, in modo da renderne la superficie più raffinata. Una smerigliatrice piana è una macchina utensile progettata per fornire superfici di rettifica precise, sia di dimensioni critiche che di finitura superficiale. La precisione specifica della smerigliatrice piana dipende dal tipo e dall'utilizzo, il diametro del disco è di 300 mm, la precisione planimetrica può raggiungere 0,003 mm. La dimensione massima di lavorazione della rettifica piana: lunghezza 1600* larghezza 800 mm.
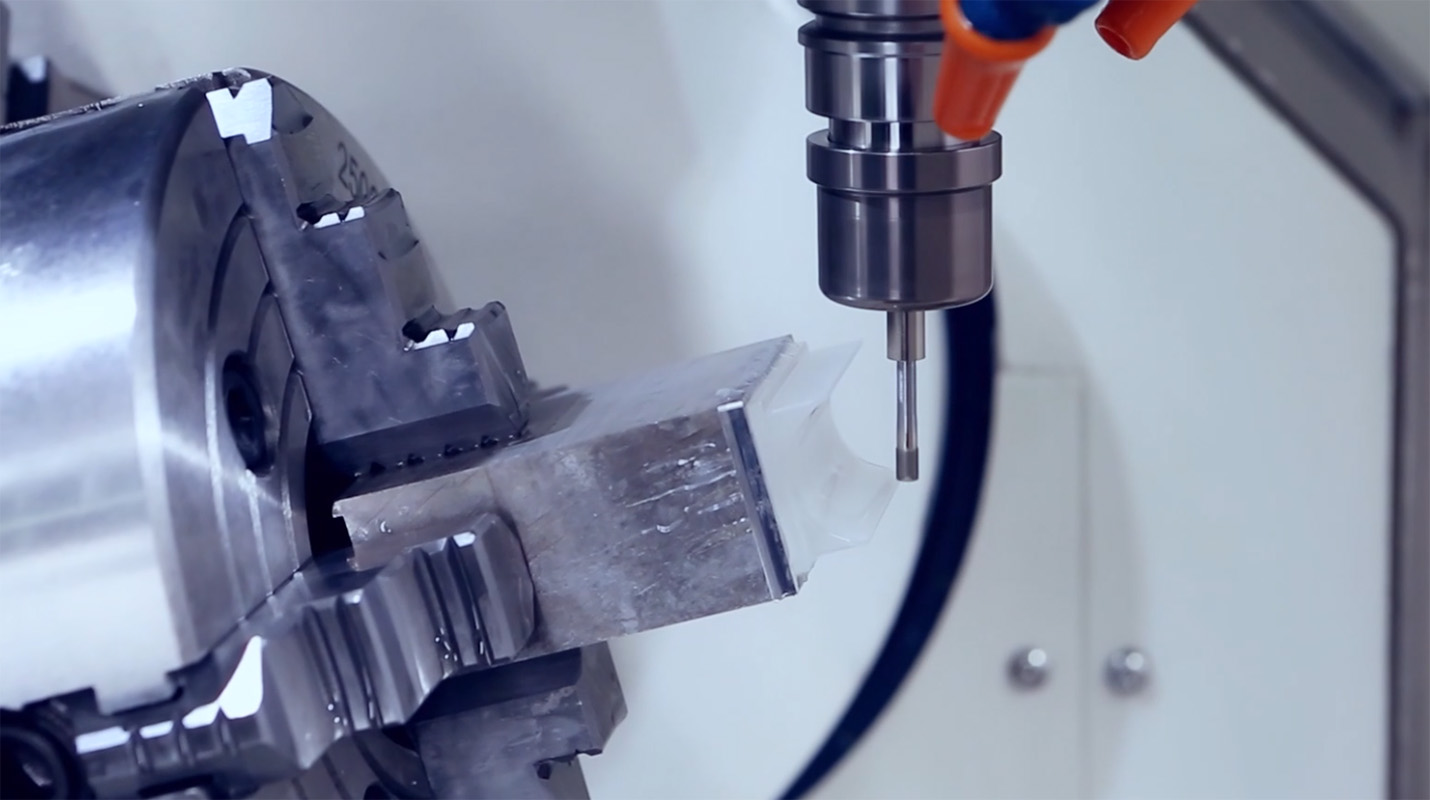
CNC
La fresatura CNC è considerata una delle operazioni più utilizzate nella lavorazione meccanica. La fresatura CNC è un tipo di macchina utensile CNC con una forte funzione di elaborazione, il centro di lavoro a sviluppo rapido, l'unità di lavorazione flessibile, ecc. sono prodotti sulla base della fresatrice CNC e dell'alesatrice CNC, entrambi sono inseparabili dal metodo di fresatura, la maggior parte industriale le operazioni di fresatura possono essere completate da macchine utensili CNC a 3 e 5 assi. Con i vantaggi di forte adattabilità, elevata precisione di lavorazione, qualità di lavorazione stabile ed elevata efficienza produttiva, questo tipo di controllo del percorso può elaborare fino all'80% delle parti meccaniche. Il CNC ha una dimensione massima di lavorazione: lunghezza 1300* larghezza 800 mm.
Processo di pulizia dei componenti semiconduttori
Pulizia a umido
La pulizia a umido consiste nell'uso di solventi chimici o acqua deionizzata per pulire il wafer. La pulizia a umido può essere suddivisa in metodo di ammollo e metodo di spruzzatura in base al metodo di processo, il metodo di ammollo consiste nell'immergere il wafer in un serbatoio contenente solvente chimico o acqua deionizzata. Il metodo di ammollo è un metodo ampiamente utilizzato, soprattutto per alcuni nodi maturi. La spruzzatura, invece, comporta la spruzzatura di un solvente chimico o di acqua deionizzata su un wafer rotante per rimuovere le impurità. Il metodo di immersione può elaborare più wafer contemporaneamente, mentre il metodo di spruzzatura può elaborare contemporaneamente solo un wafer in una camera di lavoro. Con lo sviluppo del processo, i requisiti del processo di pulizia stanno diventando sempre più elevati e l'uso del metodo di spruzzatura sta diventando sempre più ampio.
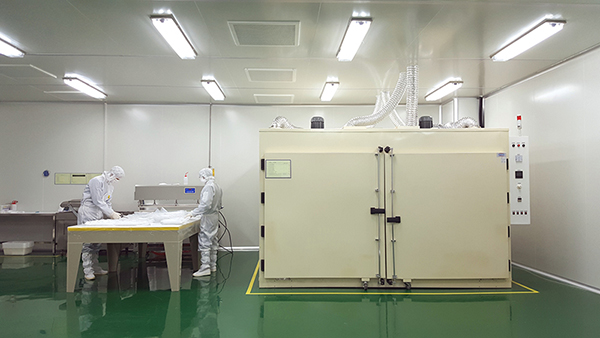
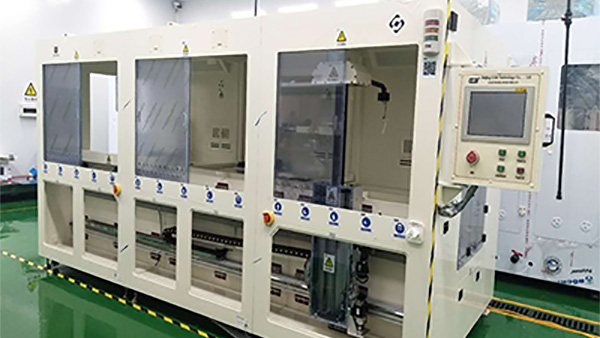
Lavaggio a secco
Come suggerisce il nome, il lavaggio a secco non prevede l'uso di solventi chimici o acqua deionizzata, ma l'uso di gas o plasma per pulire. Con il continuo avanzamento dei nodi tecnici, i requisiti del processo di pulizia stanno diventando sempre più elevati, anche la percentuale di utilizzo è in aumento e anche il liquido di scarto generato dalla pulizia a umido è in notevole aumento. Rispetto al lavaggio a umido, il lavaggio a secco presenta costi di investimento elevati, funzionamento complesso delle apparecchiature e condizioni di pulizia più difficili. Tuttavia, per la rimozione di alcuni composti organici e nitruri, ossidi, la precisione del lavaggio a secco è maggiore e l'effetto è eccellente.
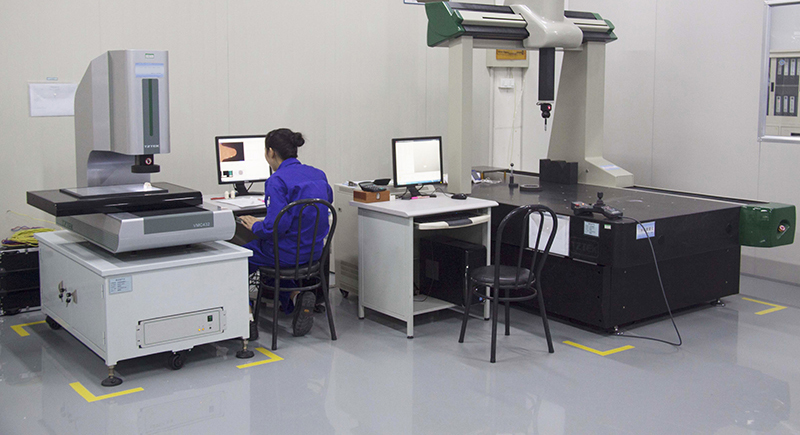
Misurazione di precisione
Abbiamo talento nella ricerca sui materiali, nello sviluppo del prodotto, nella progettazione, nella produzione e nella gestione della qualità e disponiamo di una serie completa di apparecchiature di lavorazione e collaudo di precisione: tre coordinate, rugosimetro, misuratore di concentricità, strumento di misurazione del diametro esterno, misuratore di cilindricità di strumenti di prova di precisione. Processo di produzione rigoroso e apparecchiature di produzione e collaudo ad alta precisione per garantire l'alta qualità dei prodotti.
Rivestimento DLC
I tavoli portawafer/pinza vengono utilizzati per contenere Si, SiC, GaAs, Gan e altri wafer semiconduttori in una varietà di processi di semiconduttori, dal rilevamento alla litografia e altre applicazioni esigenti di alta precisione, compreso l'alloggiamento di display a schermo piatto flessibili, grandi e sottili , MEMS e cellule biologiche. I rivestimenti DLC hanno molte proprietà desiderabili, come resistenza durevole ed elevata conduttività termica, per massimizzare la durata del prodotto, mantenere la precisione e ridurre l'attrito e la contaminazione. La pinza a vuoto è costituita da un corpo rigido con pinze multiple sulla superficie del wafer o del pannello, e la deviazione della planarità complessiva e locale viene misurata in nanometri, in questo caso il problema con l'applicazione di un rivestimento DLC su tutta la superficie del la pinza è che la mancata corrispondenza dell'espansione termica può portare a una perdita di planarità.
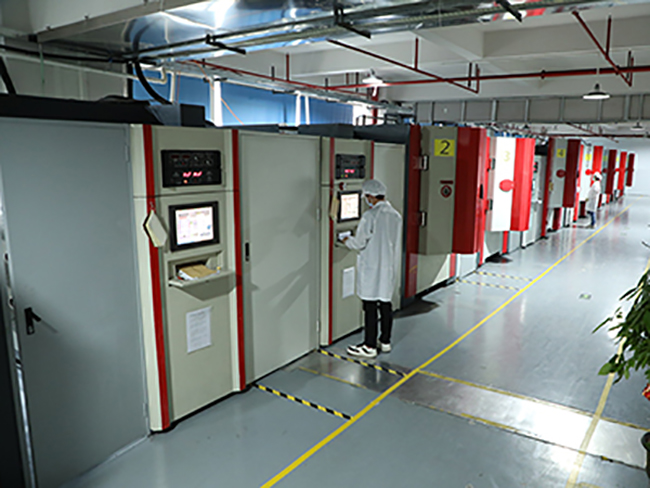
Fluoropolimero Teflon™ per la produzione di semiconduttori
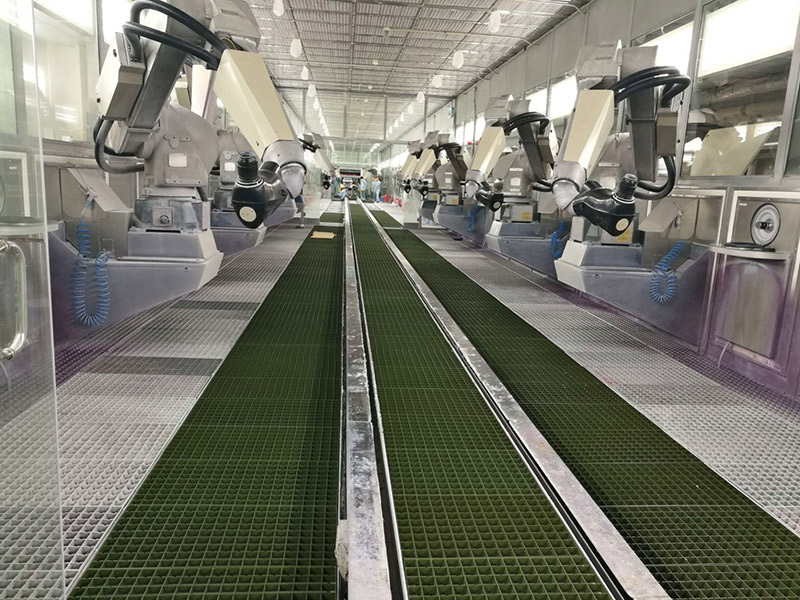