Produktionstechnologie
Strenger Produktionsprozess und hochpräzise Produktions- und Prüfgeräte gewährleisten die hohe Qualität der Produkte.
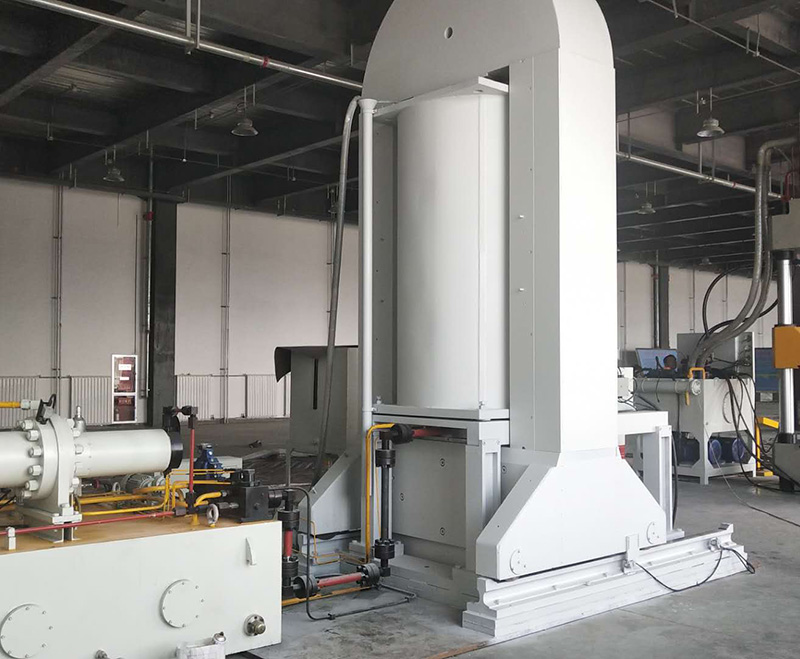
Trockenpressverfahren
Trockenpressen ist eines der am weitesten verbreiteten Formverfahren. Die Hauptvorteile sind eine hohe Formeffizienz, geringe Größenabweichung der Formprodukte, besonders geeignet für eine Vielzahl von Keramikprodukten mit geringer Querschnittsdicke, wie z. B. Keramikventilkerne, Keramikplatten und Keramik klingeln...usw.
Isostatisches Pressverfahren und Eigenschaften
Das isostatische Pressformen hat gegenüber dem Stahlformpressformen die folgenden Vorteile:
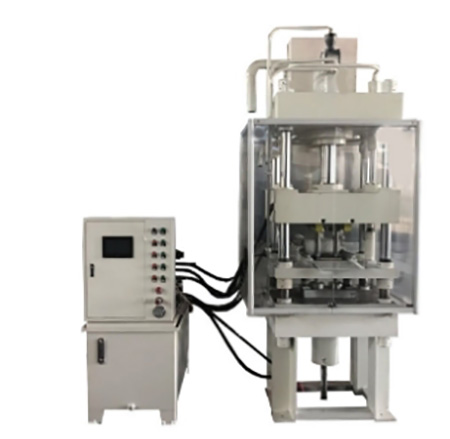
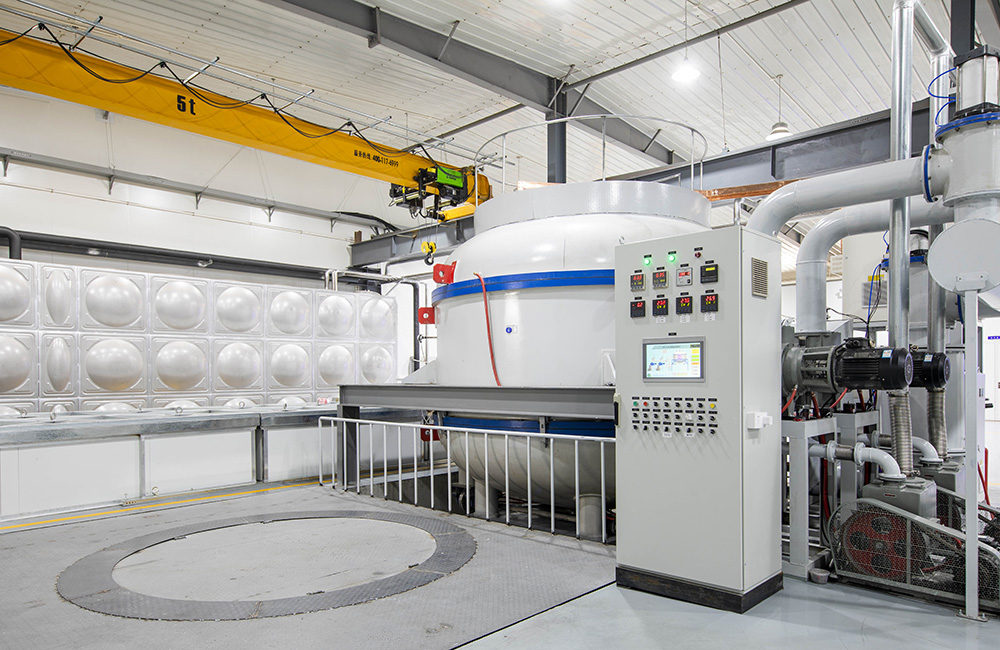
Keramiksintern
Der Keramikrohling besteht vor dem Sintern aus vielen einzelnen Feststoffpartikeln, es gibt eine große Anzahl von Poren im Körper, die Porosität beträgt im Allgemeinen 35 % bis 60 % (d. h. die relative Dichte des Rohlings beträgt 40 % bis 65 %). Der spezifische Wert hängt von den Eigenschaften des Pulvers selbst sowie der verwendeten Formungsmethode und -technologie ab. Wenn der massive Rohling auf eine hohe Temperatur erhitzt wird, übertragen sich die Partikel im Rohling, nach Erreichen einer bestimmten Temperatur schrumpft der Rohling, es kommt zu Kornwachstum, begleitet von der Beseitigung von Poren, und schließlich wird der Rohling zu einem dichten polykristallinen Keramikmaterial Bei einer Temperatur unterhalb des Schmelzpunktes nennt man diesen Vorgang Sintern.
Innen- und Außenrundschleifen
Beim Innen- und Außenrundschleifen (auch Zentrumsschleifen genannt) werden die äußere Kreisfläche und die Schulter des Werkstücks geschliffen. Das Werkstück ist in der Mitte montiert und wird von einer Vorrichtung namens Zentrumsmitnehmer gedreht. Schleifscheiben und Werkstücke werden von separaten Motoren mit unterschiedlichen Geschwindigkeiten gedreht. Die Klemmposition des Produkts kann in einem Winkel eingestellt werden, um eine Konizität zu erzeugen. Es gibt fünf Arten des Schleifens von Außendurchmessern (OD), Schleifen von Innendurchmessern (ID), Stempelschleifen, Tiefschleifen und spitzenloses Schleifen.
Außendurchmesserschleifen
Beim Außendurchmesserschleifen wird die Außenfläche eines Objekts zwischen der Mitte und der Mitte geschliffen. Das Zentrum ist eine Endzelle mit einem Punkt, der die Drehung des Objekts ermöglicht. Wenn die Schleifscheibe das Objekt berührt, dreht sich auch die Schleifscheibe in die gleiche Richtung. Dies bedeutet effektiv, dass sich die beiden Oberflächen bei Kontakt in entgegengesetzte Richtungen bewegen, was den Betrieb stabiler und weniger blockierend macht.
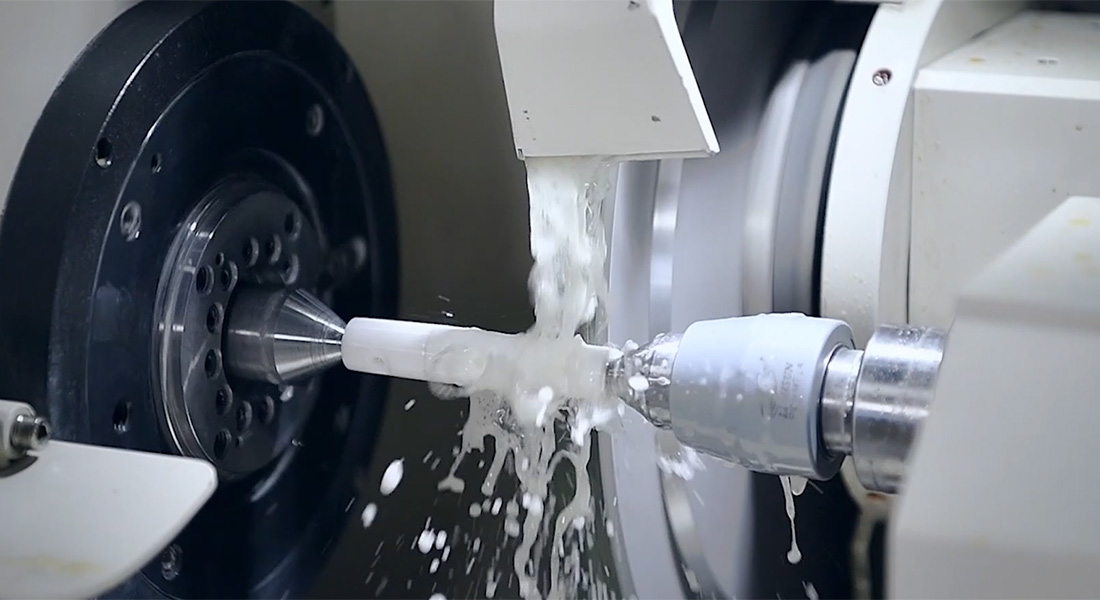
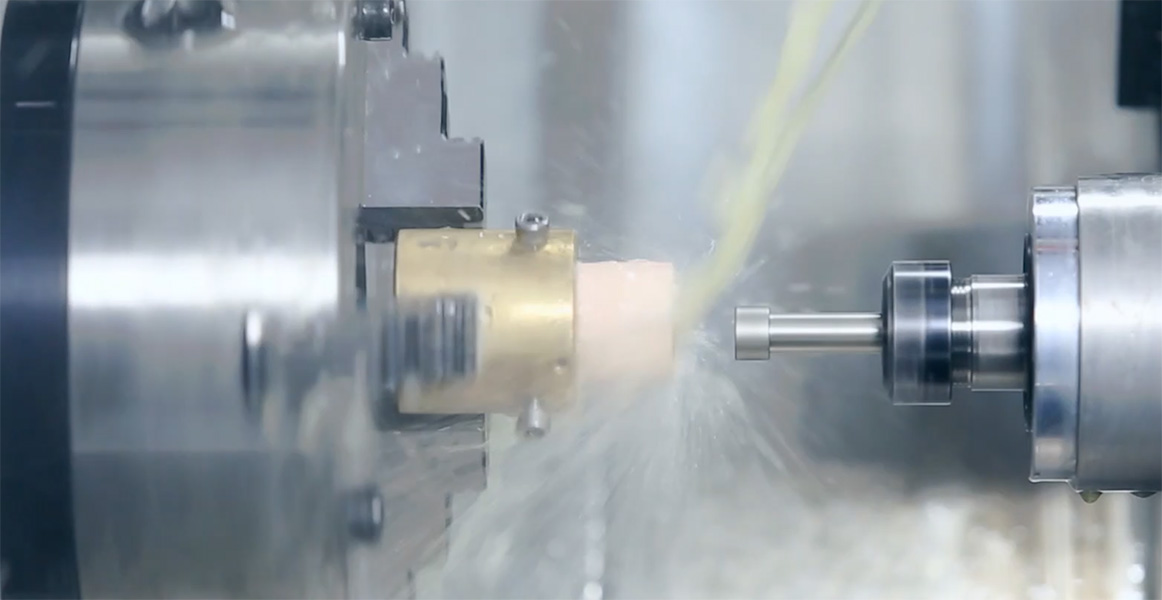
Innendurchmesserschleifen
Beim Innendurchmesserschleifen wird das Innere eines Objekts geschliffen. Die Breite der Schleifscheibe ist immer geringer als die Breite des Objekts. Das Objekt wird durch die Vorrichtung an Ort und Stelle gehalten, die es auch an Ort und Stelle dreht. Genau wie beim Außendurchmesserschleifen drehen sich die Scheibe und das Objekt in entgegengesetzte Richtungen, sodass die Kontaktrichtung der beiden Oberflächen, auf denen geschliffen wird, entgegengesetzt ist.
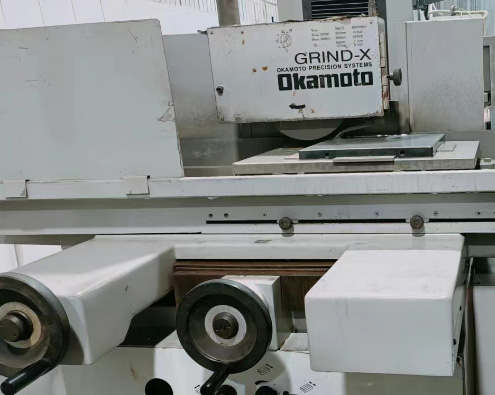
Flachschleifen
Das Flachschleifen ist der häufigste Schleifvorgang. Es handelt sich um eine Verarbeitungstechnologie, bei der eine rotierende Schleifscheibe zum Schleifen der Oberfläche von metallischen oder nichtmetallischen Materialien verwendet wird, um die Oxidschicht und Verunreinigungen auf der Oberfläche des Werkstücks zu entfernen und so die Oberfläche zu verfeinern. Ein Flachschleifer ist eine Werkzeugmaschine, die zum präzisen Schleifen von Oberflächen entwickelt wurde, unabhängig davon, ob es sich um eine kritische Größe oder um eine Oberflächenbeschaffenheit handelt. Die spezifische Genauigkeit des Flachschleifers hängt von seiner Art und Verwendung ab, der Scheibendurchmesser beträgt 300 mm, die planimetrische Genauigkeit kann 0,003 mm erreichen. Die maximale Bearbeitungsgröße beim Flachschleifen: Länge 1600* Breite 800mm.
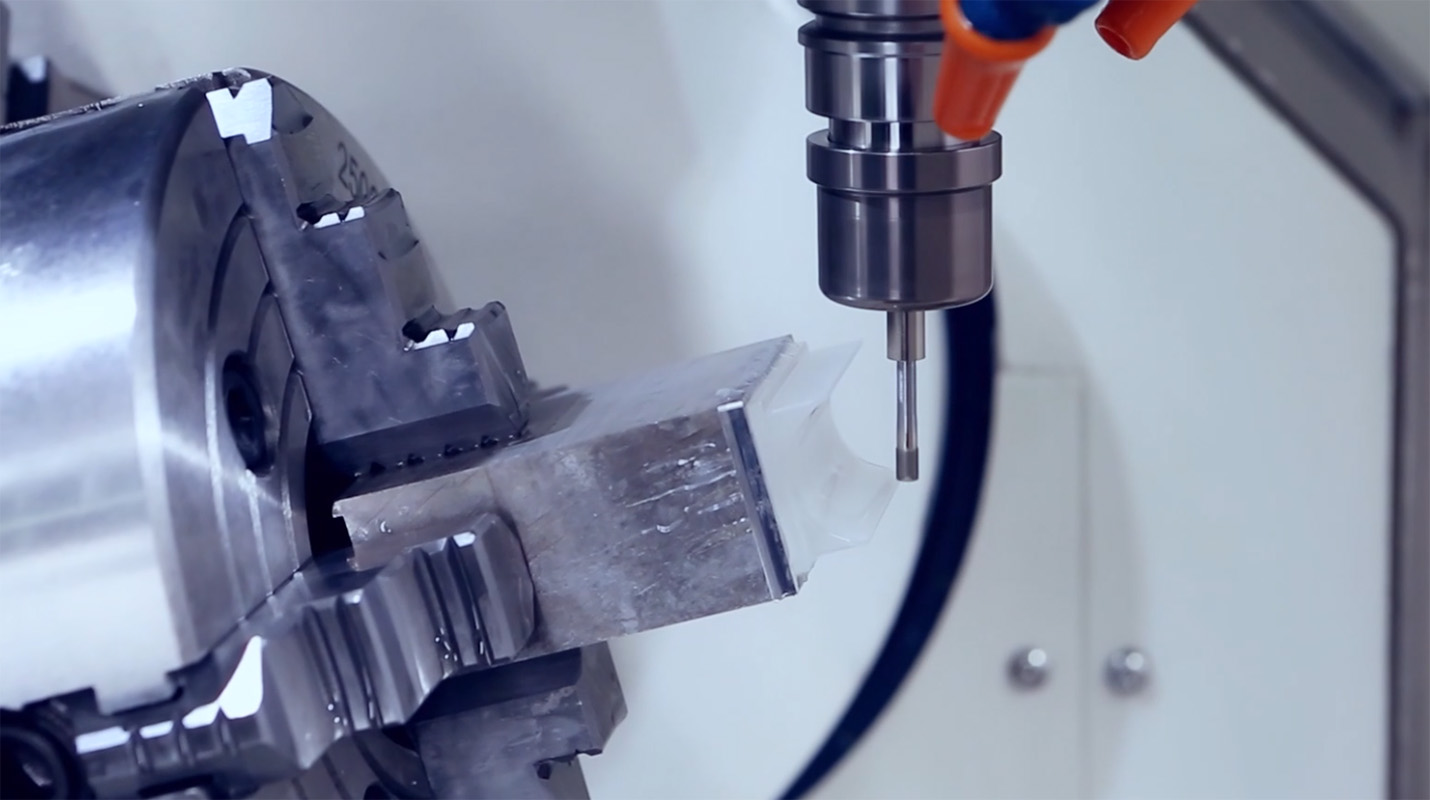
CNC
Das CNC-Fräsen gilt als einer der am weitesten verbreiteten Bearbeitungsvorgänge. CNC-Fräsen ist eine Art CNC-Werkzeugmaschine mit starker Bearbeitungsfunktion. Das schnell entwickelte Bearbeitungszentrum, die flexible Bearbeitungseinheit usw. werden auf der Basis von CNC-Fräsmaschinen und CNC-Bohrmaschinen hergestellt. Beide sind untrennbar mit der Fräsmethode verbunden, die meist industriell ist Fräsvorgänge können mit 3-Achsen- und 5-Achsen-CNC-Werkzeugmaschinen durchgeführt werden. Mit den Vorteilen starker Anpassungsfähigkeit, hoher Bearbeitungsgenauigkeit, stabiler Bearbeitungsqualität und hoher Produktionseffizienz kann diese Art der Bahnsteuerung bis zu 80 % der mechanischen Teile bearbeiten. CNC hat eine maximale Bearbeitungsgröße: Länge 1300 x Breite 800 mm.
Reinigungsprozess für Halbleiterkomponenten
Nassreinigung
Bei der Nassreinigung werden zur Reinigung des Wafers chemische Lösungsmittel oder entionisiertes Wasser verwendet. Die Nassreinigung kann je nach Prozessmethode in Einweichmethode und Sprühmethode unterteilt werden. Bei der Einweichmethode wird der Wafer in einen Behältertank eingetaucht, der chemisches Lösungsmittel oder entionisiertes Wasser enthält. Die Einweichmethode ist eine weit verbreitete Methode, insbesondere für einige reife Knoten. Beim Sprühen hingegen wird ein chemisches Lösungsmittel oder entionisiertes Wasser auf einen rotierenden Wafer gesprüht, um Verunreinigungen zu entfernen. Mit der Einweichmethode können mehrere Wafer gleichzeitig bearbeitet werden, mit der Sprühmethode kann jeweils nur ein Wafer in einer Arbeitskammer bearbeitet werden. Mit der Weiterentwicklung des Verfahrens werden die Anforderungen an den Reinigungsprozess immer höher und der Einsatz von Sprühverfahren immer umfangreicher.
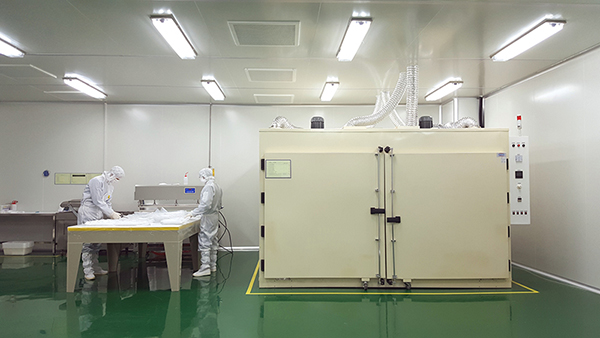
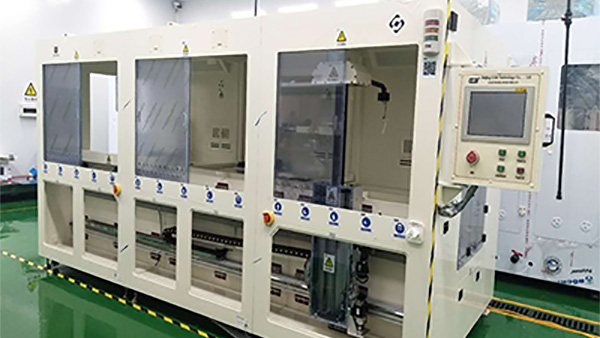
Chemische Reinigung
Wie der Name schon sagt, handelt es sich bei der Trockenreinigung nicht um den Einsatz von chemischen Lösungsmitteln oder entionisiertem Wasser, sondern um die Verwendung von Gas oder Plasma zur Reinigung. Mit der kontinuierlichen Weiterentwicklung der technischen Knoten werden die Anforderungen an den Reinigungsprozess immer höher, auch der Nutzungsanteil steigt und auch die bei der Nassreinigung anfallende Abfallflüssigkeit nimmt stark zu. Im Vergleich zur Nassreinigung ist die Trockenreinigung mit hohen Investitionskosten, komplexer Gerätebedienung und härteren Reinigungsbedingungen verbunden. Bei der Entfernung einiger organischer Verbindungen sowie Nitride und Oxide ist die Genauigkeit der Trockenreinigung jedoch höher und die Wirkung hervorragend.
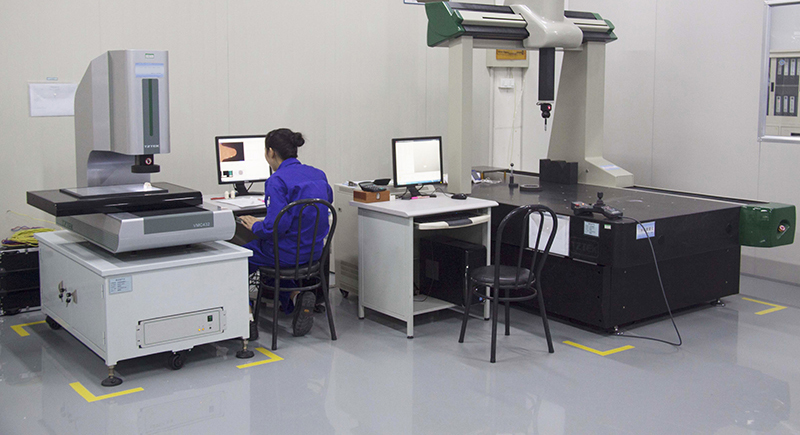
Präzisionsmessung
Wir verfügen über Talente in den Bereichen Materialforschung, Produktentwicklung, Design, Fertigung und Qualitätsmanagement und verfügen über ein komplettes Set an Präzisionsbearbeitungs- und Prüfgeräten: drei Koordinaten, Rauheitsmessgerät, Konzentrizitätsmessgerät, Außendurchmessermessgerät, Zylindrizitätsmessgerät und Präzisionsprüfgeräte. Strenger Produktionsprozess und hochpräzise Produktions- und Prüfgeräte gewährleisten die hohe Qualität der Produkte.
DLC-Beschichtung
Wafer-Träger-/Greifertische werden zur Aufnahme von Si-, SiC-, GaAs-, Gan- und anderen Halbleiterwafern in einer Vielzahl von Halbleiterprozessen verwendet, von der Erkennung bis zur Lithographie und anderen hochpräzisen anspruchsvollen Anwendungen, einschließlich der Unterbringung großer, dünner, flexibler Flachbildschirme , MEMS und biologische Zellen. DLC-Beschichtungen verfügen über viele wünschenswerte Eigenschaften, wie dauerhafte Beständigkeit und hohe Wärmeleitfähigkeit, um die Produktlebensdauer zu maximieren, die Genauigkeit aufrechtzuerhalten und Reibung und Verschmutzung zu reduzieren. Der Vakuumgreifer besteht aus einem starren Körper mit mehreren Greifern auf der Oberfläche des Wafers oder Panels, und die Abweichung der Gesamt- und lokalen Ebenheit wird in Nanometern gemessen, in diesem Fall das Problem beim Aufbringen einer DLC-Beschichtung auf der gesamten Oberfläche Der Greifer besteht darin, dass die nicht übereinstimmende Wärmeausdehnung zu einem Verlust der Ebenheit führen kann.
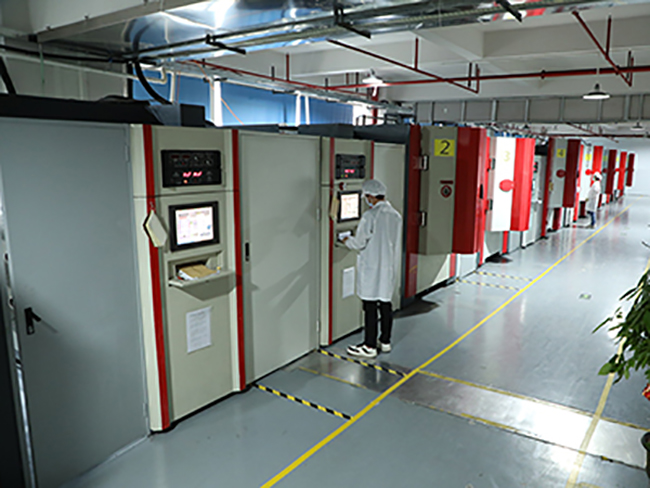
Teflon™ Fluorpolymer für die Halbleiterfertigung
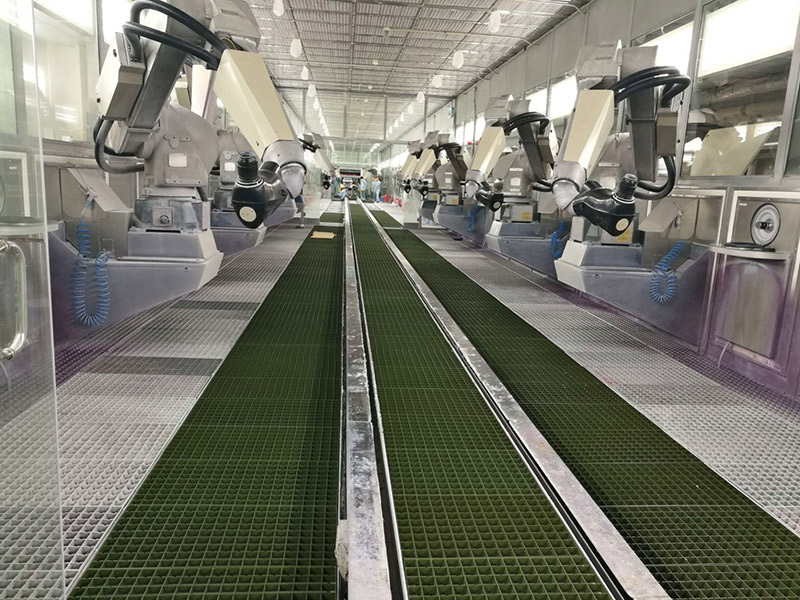